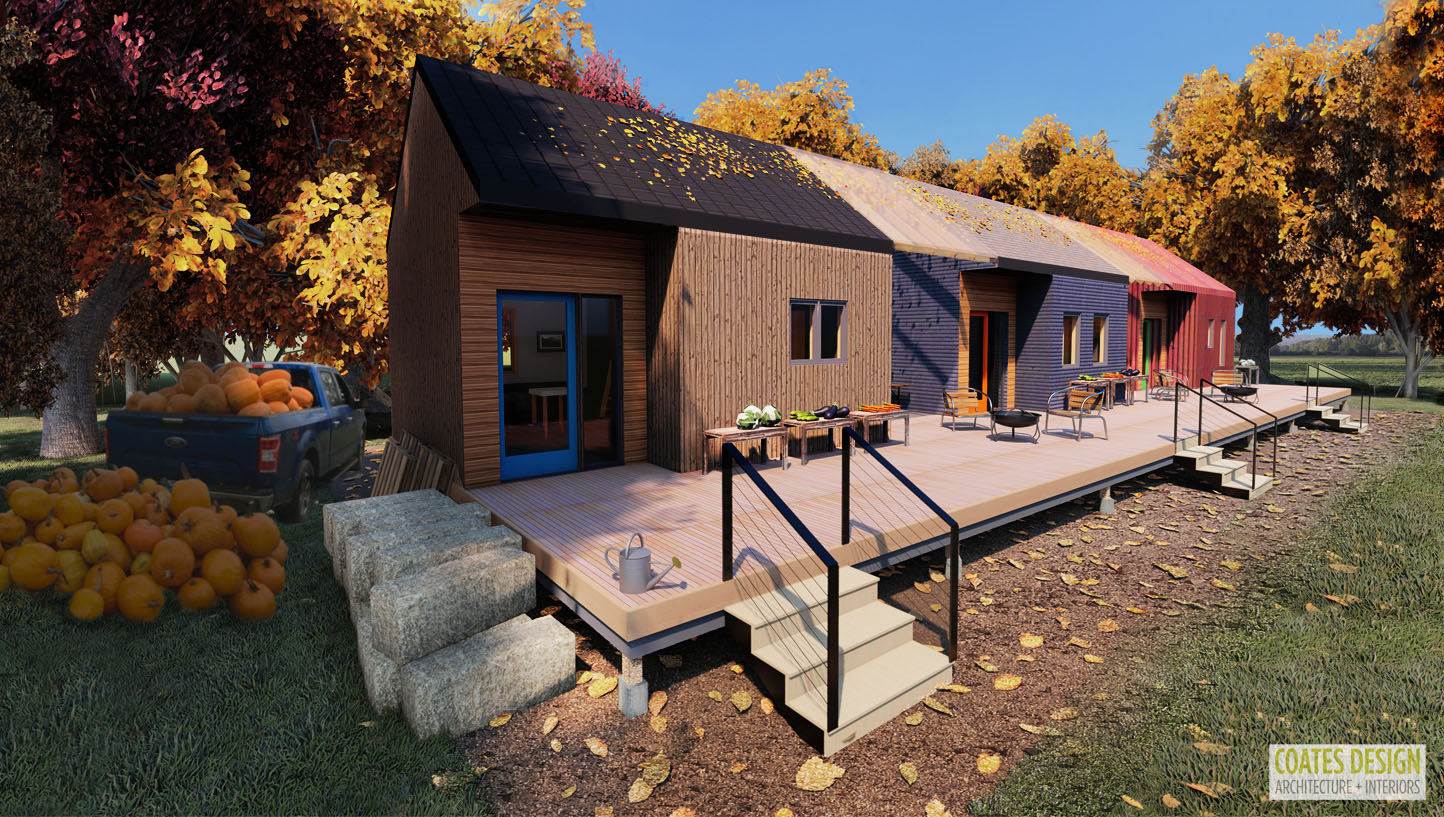
Architect Matthew Coates thinks affordable housing can be created using only cast-off construction materials and appliances.
The founder of Bainbridge Island-based Coates Design Architects is putting that to the test by designing three tiny housing units using materials that are 100% recycled, reclaimed or unwanted, or that would otherwise be headed to the landfill.
The 220-square-foot units will be on Morales Farm, a farmland property at 8862 N.E. Lovgreen Road owned by the city of Bainbridge Island and managed by local nonprofit Friends of the Farms. Some interns who work with area farmers will stay in the housing, for which the farmers will pay Friends rent.
Heather Burger, Friends executive director, said what little housing the island has is unaffordable to many people. Quoting Redfin, she said the median sale price of Bainbridge homes in June was $1.2 million, up 38.1% compared to last year.
“There are very few houses on the market at any price,” she said.
The tiny housing pilot project is called reHOME. Burger estimates that, exclusive of donated items, it will cost $370,000. Of that, the project partners, Coates Design Architects and Bainbridge Island-based Clark Construction, Friends and nonprofit Housing Resources Bainbridge (HRB), are providing $270,000 in pro bono services. They hope to fund-raise another $200,000 that will be split between the project cost and maintenance and management of the property. Burger said an anonymous donor has pledged to match every donation of $1,000 or more, with no limit.
HRB is providing project management and affordable housing expertise. Clark is building reHOME, and its employees are donating to the project budget.
Construction is expected start in 2022.
The team is seeking to permit the units as “satellite bedrooms” to the original house on Morales Farm. They will have a bedroom, open living area, sink, bathroom, shower and refrigerator. Each will differ slightly based on available materials and all will be movable, a city requirement.
Coates’ firm developed software — a “glorified database” — to track and document materials and services needed, such as sinks and siding and electrical and plumbing.
He said the reHOME team is spreading a “dragnet” through the local construction industry for donations and scouring websites for free or for-sale items. For instance, Builders FirstSource donated a truck load of lumber that had become weathered from sitting outside too long and Hanley Roofing pledged to donate a full coil of roofing that arrived in the wrong color — what Coates calls “orphaned” materials.
“The challenging things are like concrete,” he said, because of its short shelf life. So the team will ask firms to donate concrete mix left over from other jobs.
The architect said all materials must be vetted to determine if they fit the project. “I don’t want 16 people showing up with old toilets,” he said.
The professional services for reHOME are donated or provided at a significant discount, he said.
Coates Design Architects’ work ranges from public institutional to private homes, with projects that include the Bainbridge Island Museum of Art, the first LEED gold-certified museum in the country (new construction); Platinum House, the first LEED platinum residence in Washington outside of Seattle; and a net-zero cabin in Cle Elum.
Matthew Coates said he has been mulling a reHOME-like project for about 10 years as the need for affordable housing on the island grew and he saw people demolishing houses to build new — with a lot of the waste hauled to the dump.
The architect said the industry needs to see construction “waste” as a potential resource. Quoting the Environmental Protection Agency, he said it makes up 30% of the waste going into Washington landfills. Also quoting the agency, he said an estimated 600 million tons of construction and demolition waste was created in the United States in 2018.
Coates projects reHOME will cost one-third less to build than a typical similar project, and believes the model and cost savings could be scaled up to larger, full-size housing projects.
Clark Construction typically works in multifamily, mixed-use, commercial and high-end custom residential projects. It joined the reHOME team because sustainability is a big part of its business model, said company president Jeff Krueger. He said the industry needs to work harder to put to good use salvageable material from building projects. “What do you see on every jobsite? You see a job trailer and a dumpster.”
Many valuable materials are wasted even on projects that accept donations and surplus items, because they do not fit the design, he said. Instead, he said, Coates is making the reHOME units utilitarian — and attractive — while “designing around the materials not making the materials beholden to the design.”
Or as Coates put it, “My job is to make it look beautiful and not like something that was put together out of a junkyard.”
Krueger said he believes the reHOME approach “is something that could be scalable and replicable.”
Coates said he doesn’t know of another codified livable structure that has been made entirely of recycled, reclaimed or otherwise unwanted materials.
When the reHOME project is complete, the team plans to open source the techniques, information and technology in the hopes that others will use and perhaps improve upon it to create affordable housing in their communities, Coates said.
For now, it is figuring out the pilot project as it goes along. “This is proof of concept,” said Coates. “We absolutely expect to learn a lot.”
Full article found at:
“Bainbridge architect is using unloved materials to fashion affordable housing,” Seattle Daily Journal of Commerce, August 5, 2021.